Soil Compaction and Rolling Resistance Evaluation of a Locomotion System with an Adjustable Contact Patch for a Grape Transporting Robot
- DOI
- 10.2991/jrnal.k.191202.002How to use a DOI?
- Keywords
- Soil compaction; rolling resistance; finite element method; cone penetrometer
- Abstract
Soil compaction is a form of soil degradation which causes soil erosion, drainage difficulties, and loss of nutrients. To mitigate this issue, in agricultural farms several methods have been adopted. In this paper, the preliminary study of a locomotion system with adjustable contact patches is proposed. Aim is to reduce the compaction and optimize the rolling resistance of a grape transporting robot used in vineyard. A Finite Element Method (FEM) model supported by experimental results is developed to study the system.
- Copyright
- © 2019 The Authors. Published by Atlantis Press SARL.
- Open Access
- This is an open access article distributed under the CC BY-NC 4.0 license (http://creativecommons.org/licenses/by-nc/4.0/).
1. INTRODUCTION
Soil compaction of agricultural soil is the result of the increase in mechanization and the usage of heavy vehicles exerting high forces onto the soil. As a porous material, soil consists of a solid part which includes pores containing air or water. Excessive compression causes the reduction of pore space and the loss of air and water, important for plants roots growth, and determines infiltration difficulties, loss of nutrients and soil erosion. Soil compaction resulted to be related to a significant reduction in the yield, and it was estimated a crop yielding reduction of 25–50% in some districts of Europe and North America [1]. To solve these issues many methods have been proposed, with different results and different costs [2]. The problem can be addressed by direct interventions, such as subsoiling and plough, or by avoiding compaction using low ground pressure tyres, tracked tractors or Controlled Traffic Farming (CTF). Avoiding the compaction resulted to be the best solution in terms of cost benefits. With CTF, not only compaction itself is avoided, but energy consumption is contained because of the lower rolling resistance of vehicles on permanent traffic lane [2]. Different levels of mechanization can be adopted, depending on the type of farm, and soil compaction is often neglected by farmers.
Target of this work is the canopied vineyard, in which the trees form a roof and the small and closed environment makes more difficult a full mechanization. Here harvester machines are rarely used, unlike the espalier vineyards where big harvester machines are widely used. Usual tractors do not improve the harvesting process, but they still cause a lot of compaction.
The system proposed here consists of an autonomous mobile kart aimed to optimize the rolling resistance while avoiding the soil compaction. It consists of four small track modules which can be partially lifted so as to reduce their contact patch and act as a wheel, depending on the soil conditions and vehicle payload (Figure 1). Tracks are more suited for soft or wet soils, while wheels show better performance on hard soils.
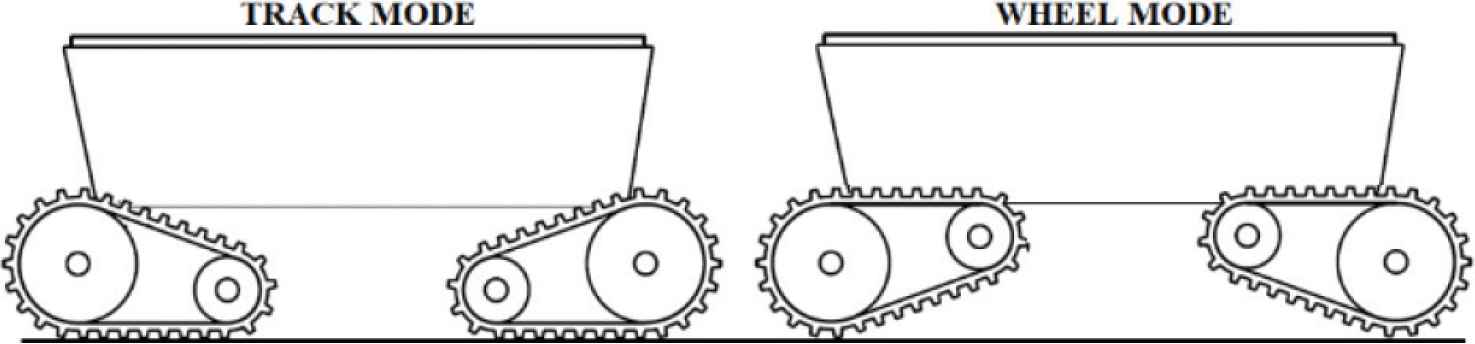
System configurations in track and wheel mode.
In this paper, the system is studied in terms of soil compaction and Rolling Resistance (RR), evaluated by empirical equations and a Finite Element Method (FEM) model. FEM simulations have been widely used for RR evaluation on soft and hard soils [3]. Experiments in the field are carried out to find some of the parameters required for modelling the soil with FEM.
Empirical equations for RR evaluation, derived from Terramechanics, are considered in the second section. In the third section, the experiments carried out in the vineyard are explained. These results, together with a non-linear regression equation, are used in Section 4 for evaluating the soil Young moduli and developing the FEM model for the analyses. Finally, in Section 5, the simulations are carried out and the results explained.
2. ROLLING RESISTANCE ON SOFT SOILS
Rolling resistance on soft terrains can be seen as the work done in compacting the soil and making a rut of area A and depth z [4], as expressed by Equation (1):
Ground contact length (mm) | 400 |
Width (mm) | 200 |
Outer sprocket diameter (mm) | 370 |
Load bearing (kg) | 100 |
HS-200 Track module
Considering this track module and a vehicle weight of 400 kg, for a CI between 500 and 7000 kPa the comparison in terms of RR between track mode and wheel mode is shown in Figure 2.
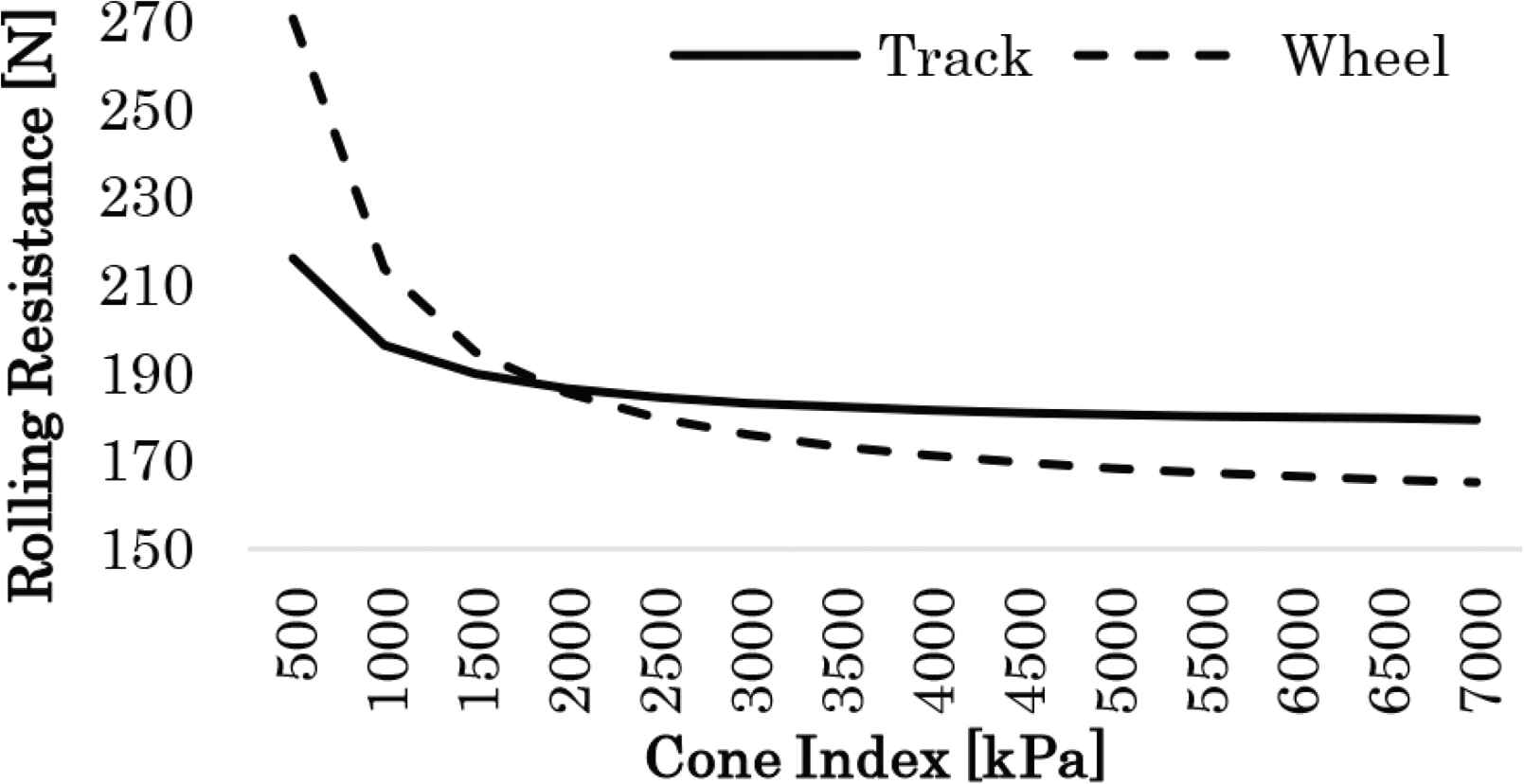
Rolling resistance comparison between wheel and track mode for different soil strengths.
As expected, on soft soil tracks outperform wheels, while on hard soil wheels have better performance.
The difference of performance between the two modes depends on track sizes and vehicle weight, and in the final design a set of best parameters has to be decided in order to maximize this difference and minimize the RR.
3. EXPERIMENTS IN THE VINEYARD
Soil strength measurements are carried out in a vineyard in the South of Italy, at Latiano city, in Puglia region.
Hand-held digital CP SC900 developed by Spectrum Technologies (3600, Thayer Court, Aurora, IL 60504, USA) is used. This sensor allows to investigate the soil until a depth of 45 cm and a CI of 7000 kPa. Moisture sensor VG Meter 200 (583, Vegetronix Inc, Riverton, UT 84065, USA) is adopted for measuring the volumetric water content percentage. Moisture content affects soil behavior and rolling resistance considerably, and for this reason it is important to monitor it in the analysis.
The measurements are taken with profiles 6 m apart of each other made of nine points each, as in Figure 3, so as to get a profile of compaction along the path width, with a total of 63 measurements. The distance between the trees is 2 m, while the space among each measurement point is 22 cm. The points are in the middle between the trees of each path side for avoiding their roots. Because the average CI for the first 15 cm is widely used for rolling resistance evaluation [5], a depth of 15 cm is considered here. On the wheel tramlines some of the measurements could not be completed because the resistance exceeded the limit of the sensor. In the analysis a value of 7000 kPa (sensor limit) is considered for those points.
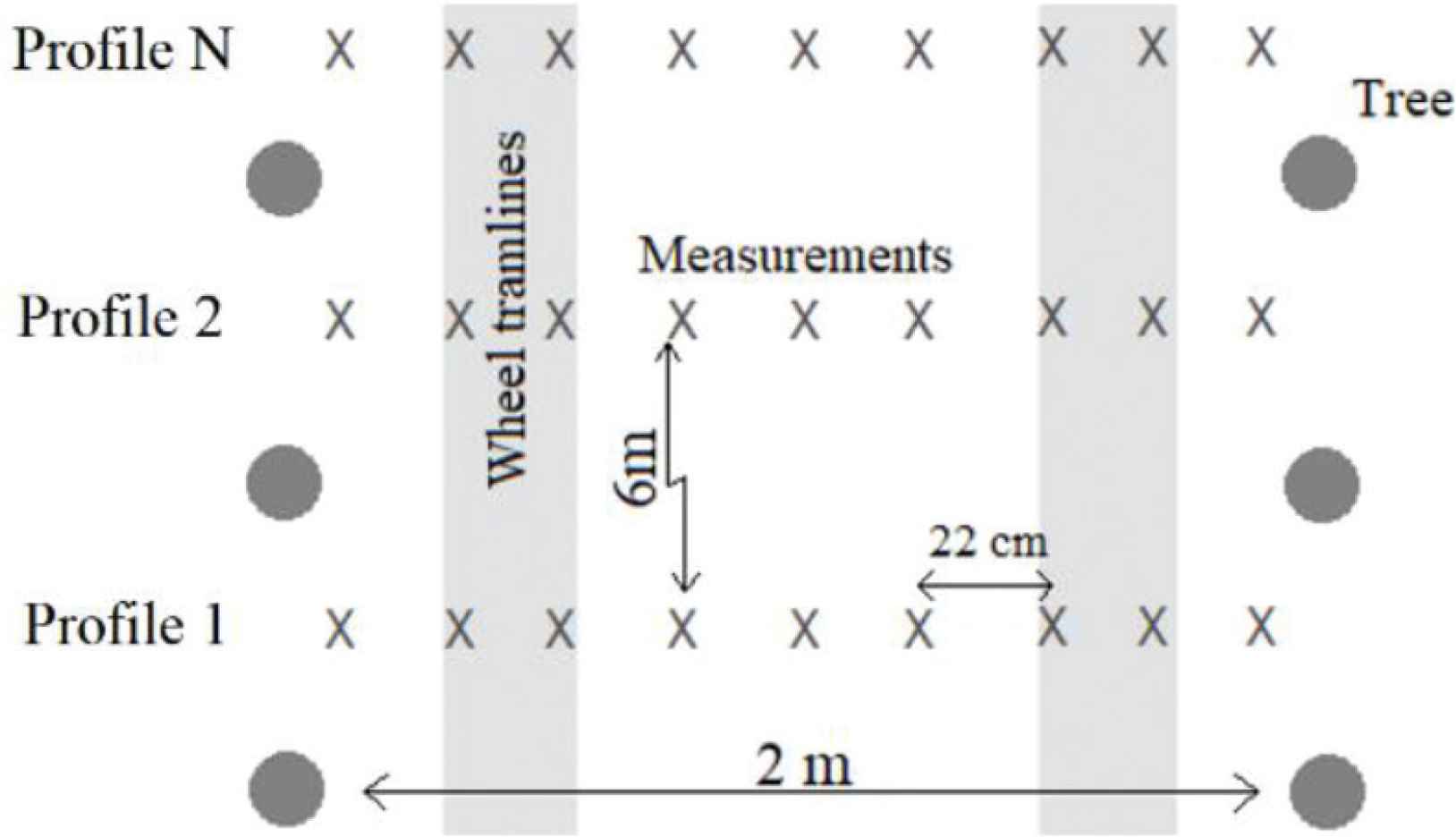
Experimental layout.
The results in terms of range of CI measured and profile along the road are reported in Figures 4 and 5 respectively. Moisture content average is of 6.5% in a range of [2–17%]. High variability in the overall CI results is due to the higher compaction at the wheel tramlines, as it can be seen from the two peaks in the strength profile.
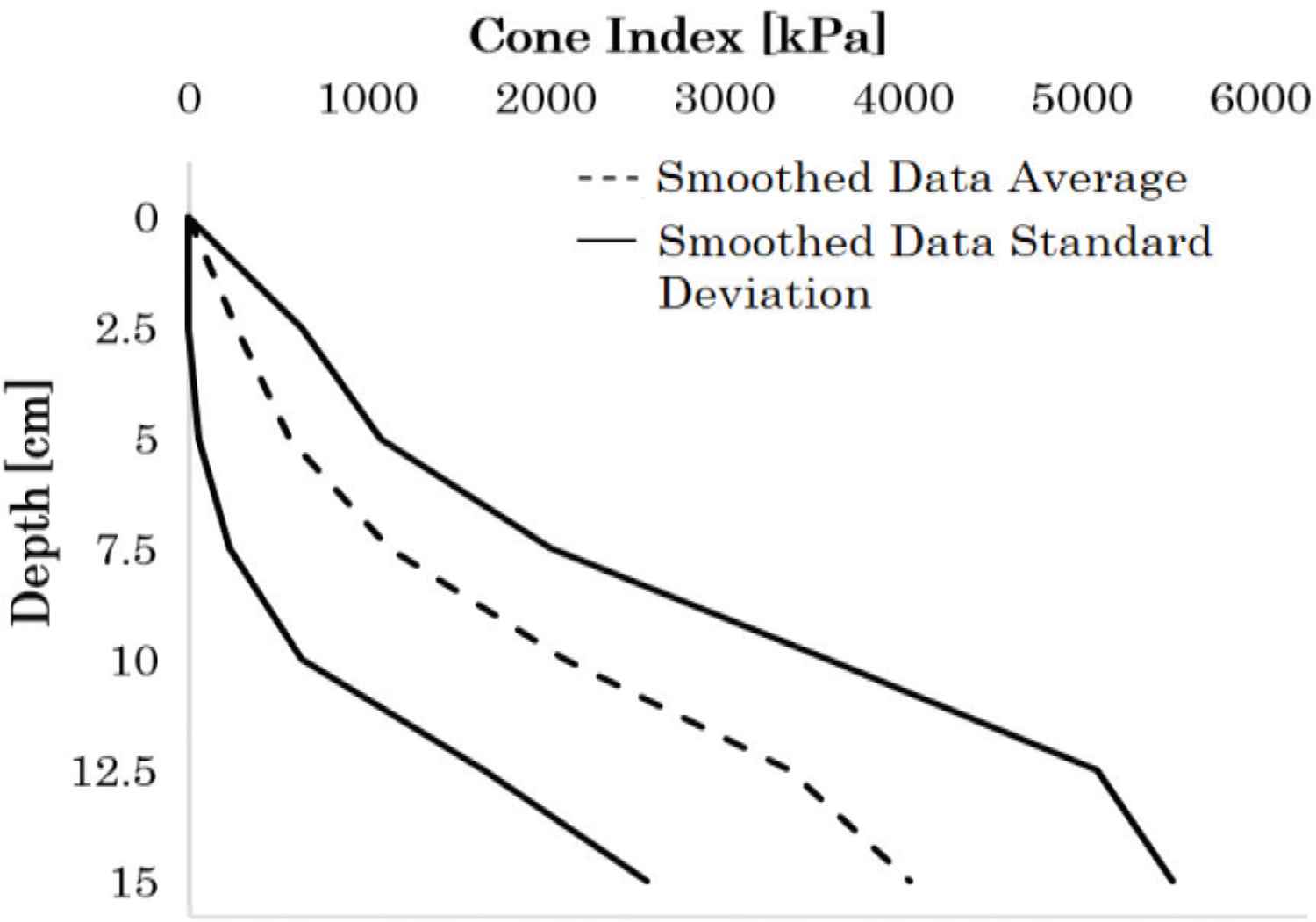
Cone index overall results.
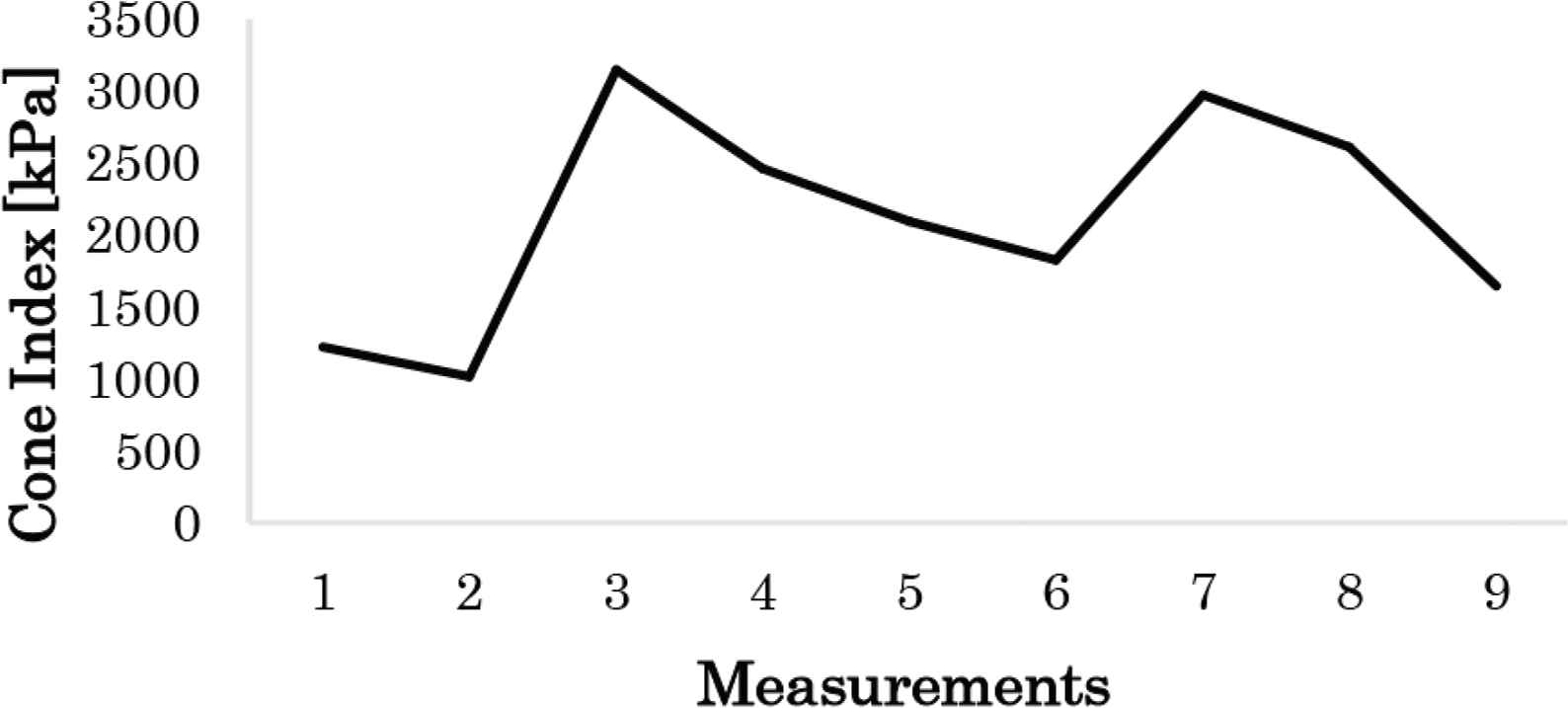
Soil strength profile AVG 15 cm.
4. SOIL MODELLING AND SIMULATIONS
Soil under stress shows an elastoplastic behavior. Drucker-Prager criterion (DP), outer cone approximation of the Mohr-Coulomb criterion, is used in this work [3].
A strategy adopted for modelling the soil using FEM is to divide it into layers. Based on the values of CI got during the experiments, three layers are modeled. First 2.5 cm with low strength, 2.5–7.5 cm with medium strength and from 7.5 to 50 cm with high strength. Density and Young Modulus E (in case of soils also called Modulus of deformation) are different in each layer. The relation between CI and E for cohesive and non-cohesive soils is provided by Mel’nikov and Boldyrev [8], by the non-linear regression equation shown in Equation (4), based on the soil classes classification as in Mel’nikov and Boldyrev [8], using a soil type function Ic. From the average CI of the experiments and considering a clay soil class, the Young moduli for the three layers are estimated.
The estimated Young moduli for the three layers are: 0.5, 4.35 and 13.1 MPa, for the first, second and third layer respectively.
As a first step soil is considered as an isotropic elastic medium [9], with the Young moduli reported above and a Poisson ratio of 0.3. The model is then completed by a bilinear isotropic hardening rule, and uniaxial compressive and tensile strength and biaxial compressive strength for the DP criterion. These last values should also be found experimentally. Tentative values taken from the literature for soft and hard clay soils are used. Additional experiments in the field are needed to tune properly these values and define a specific soil.
The FEM analysis discussed is an improved version of the analysis in di Maria and Ishii [10], where only static simulations are performed and RR resulted too underestimated.
A transient analysis is performed to take into account also the dynamic effects. The simulation consists of towing a wheel and a track on the agricultural soil modeled by FEM. The vertical weight is 1000 N with a velocity of 15 mm/s. To improve the time efficiency of each simulation a 2-D model is adopted instead of a 3-D model.
5. RESULTS AND DISCUSSION
The outputs evaluated by the FEM analysis are: the sinkage, the RR and the soil stress. For the wheel mode the steady-state value of the sinkage is 11.3 mm with a RR between 83 and 86 N. Soil stress has a peak of 62.7 kPa at a depth of 2.5 cm. This value decreases soon after the first layer and becomes <30 kPa at a depth of about 10 cm. For the track mode, the rut depth is 1.5 mm and RR is between 75 and 80 N. The peak of soil stress is 17.2 kPa at the first layer. Also in this case it decreases at the deeper layers. At a depth of 25 cm the stress is about 15.5 kPa for the wheel and 11 kPa for the track. This behavior is in agreement with other analyses [2], for which the contact pressure affects mainly the first layers, while the stress at the deeper layers depends mainly on the vertical load. Values of RR are close for both the locomotion modes. With an average CI of 1800 kPa we can expect close values of RR for the two modes, with the size and weight chosen for the track module, as seen from the empirical equations in Section 2. But the values are still low and further model refinements are required.
6. CONCLUSIONS AND FUTURE WORKS
In this paper, the preliminary study for the development of a mobile robot with an adjustable contact area was presented. Aim of the robot is to transport the grape in the vineyard, in order to support the harvesting process by optimizing the energy consumption while reducing the soil compaction. The experimental results presented in Section 3 had a double use. At first they showed the effect of the tractors traffic in the vineyard, where the wheel tramlines were more compacted than the surrounding areas. Second, they served for estimating the Young moduli of the three soil layers in the FEM model. This model is used as a tool for the design.
The results obtained from the analysis are in agreement with the expectation, but further experiments with a real pull test in the vineyard are required to tune the parameters of the model and get more precise results. After this tuning, the model can be used to carry out an analysis for choosing the best set of design parameters in terms of track module size and robot maximum weight.
CONFLICTS OF INTEREST
The authors declare they have no conflicts interest.
ACKNOWLEDGMENTS
We thank our friend Daniele Ciccarese for allowing us to carry out the experiments in his farm and for his support.
Authors Introduction
Mr. Enrico di Maria
He received his Master degree in Mechanical Engineering from the Department of Innovation Engineering, at University of Salento, Italy, in 2016. He is pursuing the PhD at Kyushu Institute of Technology, Department of Life Science and Systems Engineering, under the supervision of Prof. Kazuo Ishii. His research interests include off-road vehicles and agricultural robots.
Prof. Kazuo Ishii
He received the PhD degree from the Department of Naval Architecture and Ocean Engineering, University of Tokyo, Tokyo, Japan, in 1996. He is currently a Professor with the Department of Human Intelligence Systems, and the Director of the Center for Socio-Robotic Synthesis, Kyushu Institute of Technology, Kitakyushu, Japan. His research interests include underwater robots, agricultural robots, roboCup soccer robots and intelligent systems.
REFERENCES
Cite this article
TY - JOUR AU - Enrico di Maria AU - Kazuo Ishii PY - 2019 DA - 2019/12/10 TI - Soil Compaction and Rolling Resistance Evaluation of a Locomotion System with an Adjustable Contact Patch for a Grape Transporting Robot JO - Journal of Robotics, Networking and Artificial Life SP - 148 EP - 151 VL - 6 IS - 3 SN - 2352-6386 UR - https://doi.org/10.2991/jrnal.k.191202.002 DO - 10.2991/jrnal.k.191202.002 ID - diMaria2019 ER -